It looks like a large, mangled drink coaster or a circular tablet from some alien race. It’s heavy enough to be used as a doorstop, and it’s filled with tooth-shaped crevices.
What is this artifact and what, in the long-forgotten dental past, was it used for?
Caulk’s Universal Die Plate, advertised through such publications as The Dental Cosmos and The Dental Brief from the late 19th century into the early 20th, was used to form crowns from metal alloys to cover teeth.
The version shown above was sold by the L. D. Caulk Dental Depot, based in Philadelphia, Pennsylvania, and another version was sold by SS White.
The Beginnings of Dental Prosthetics
To understand the importance of Caulk’s Universal Die Plate, it is essential first to grasp the evolution of dental prosthetics. Dental prosthetics have been around for centuries, with the earliest known dentures dating back to 700 BC. These ancient dentures were made from human or animal teeth. As time progressed, materials and methods evolved. By the 18th and 19th centuries, dentures were made from porcelain, ivory, and even gold.
The 20th century brought about significant advancements in dental materials and techniques. The need for precision in creating dental prosthetics became paramount. Dentists and dental technicians required reliable tools to ensure that prosthetics fit perfectly and functioned well. This need for precision paved the way for innovations such as Caulk’s Universal Die Plate.
The Invention of Caulk’s Universal Die Plate
Caulk’s Universal Die Plate was introduced in the mid-20th century by the L.D. Caulk Company, a prominent name in dental materials and equipment. The company was founded by Dr. Levin D. Caulk in 1877 in Delaware, USA. Over the years, the L.D. Caulk Company became known for its high-quality dental products.
The Universal Die Plate was designed to improve the process of creating dental crowns, bridges, and other prosthetics. Before its invention, dental technicians faced challenges in ensuring that prosthetics were an exact match to patients’ teeth. Inaccuracies could lead to discomfort, poor function, and even the need for repeated adjustments.
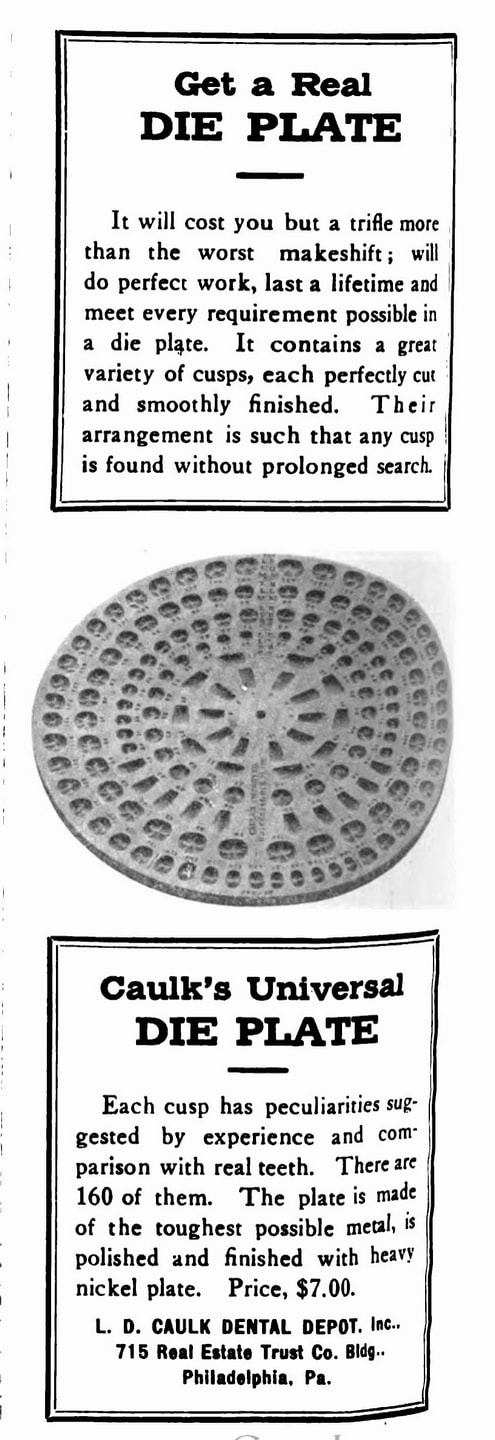
How Was the “Real Die Plate” Used?
An 1887 article from the Dental Cosmos by E. T. Star of Philadelphia titled, “Improved Die-Plate and Hubs for Shaping Metal Cap-Crowns” (left) describes the die plate process.
The die plate used to form crowns from metal alloys to cover teeth, originally resolved the universal problem of how to create lifelike (in function, not appearance) caps for damaged teeth. A crown could be made quickly, consistently, and would allow the tooth to properly function with the opposing tooth. This made the die plate quite popular in its time.
Molten Alloy and Gold Foil
The dentist poured molten alloy into a mold to make a type of plug, placed thin gold foil over one of the tooth die openings, and positioned the plug on top.
Then the dentist pounded the metal plug with a hammer until it took the form of tooth die. A dentist needed more than professional knowledge to practice in the 19th century — he needed a good right arm!
After all was said and done, the dentist had created a metal cap with a gold foil covering. Once cut out of the mold, it was ready to cap a tooth.
How Caulk’s Universal Die Plate Works
Caulk’s Universal Die Plate revolutionized the way dental prosthetics were made. It is essentially a standardized, reusable plate with multiple die spaces. Each die space is used to hold a model of a patient’s tooth or teeth. The design allows for consistent and precise replication of dental structures.
Here is a step-by-step overview of how Caulk’s Universal Die Plate is used:
- Impression Taking: The first step in creating a dental prosthetic is to take an impression of the patient’s teeth. This is done using a dental impression material that captures the exact shape and size of the teeth.
- Model Creation: The impression is then used to create a model of the patient’s teeth. This model is usually made from dental stone or plaster.
- Die Preparation: The model is sectioned to isolate the tooth or teeth that require the prosthetic. These sections, or “dies,” are placed into the spaces on the Universal Die Plate.
- Wax Pattern Creation: Using the dies as a guide, dental technicians create a wax pattern of the prosthetic. This wax pattern is a precise replica of the final prosthetic.
- Casting and Finishing: The wax pattern is then cast into the final material, such as metal or ceramic. The resulting prosthetic is finished, polished, and fitted to the patient.
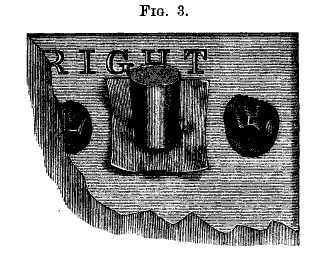
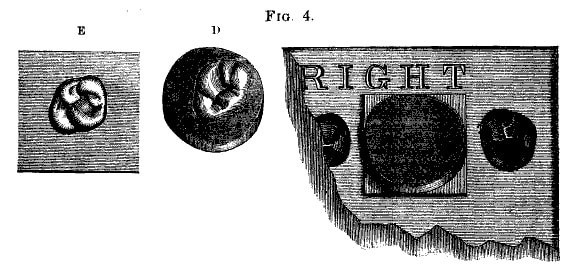
The Significance of Caulk’s Universal Die Plate
Caulk’s Universal Die Plate brought several key benefits to dental practices and laboratories:
- Precision and Accuracy: The standardized die spaces ensure that each prosthetic is made with a high degree of accuracy. This precision reduces the need for adjustments and remakes, saving time and resources.
- Consistency: The reusable nature of the die plate allows for consistent results across multiple cases. Dental technicians can rely on the die plate to produce uniform prosthetics.
- Efficiency: The streamlined process made possible by the die plate improves efficiency in dental laboratories. Technicians can work more quickly and effectively, leading to faster turnaround times for patients.
- Improved Patient Outcomes: With better-fitting and more accurate prosthetics, patients experience improved comfort and function. This leads to higher satisfaction and better overall oral health.
The Legacy of Caulk’s Universal Die Plate
Caulk’s Universal Die Plate has left a lasting legacy in the field of dentistry. Its impact can be seen in the continued emphasis on precision and accuracy in dental prosthetics. Modern dental technology has built upon the principles introduced by the Universal Die Plate, leading to even more advanced tools and techniques.
Today, digital dentistry and CAD/CAM (computer-aided design and computer-aided manufacturing) systems have taken the place of many traditional methods. These technologies allow for digital impressions, virtual models, and automated milling of prosthetics. However, the foundational concepts of precision and standardization introduced by tools like Caulk’s Universal Die Plate remain relevant.